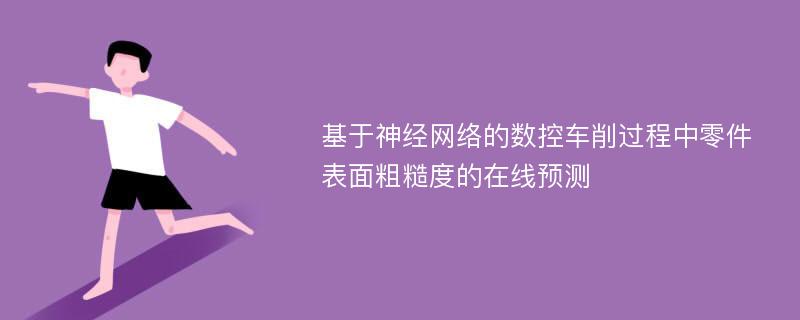
论文摘要
机械零件的表面精度是除了其尺寸精度和形状位置精度之外用于衡量零件加工质量的又一重要指标。数控机床作为先进的机械制造设备,在对产品尺寸精度和形状位置精度的控制上有着比传统机床所不可比拟的优势。然而困扰着它的自动化水平进一步提高的障碍仍然是对切削过程中零件表面粗糙度的稳定控制。本文从表面粗糙度的形成机理和评价体系入手,分析了数控精车削过程中影响表面粗糙度值的原因及切削参数与它们之间的关系,发现其主要问题是它们相互作用下所引起的刀具与工件之间的相对振动,从而产生相对偏移,导致了零件表面的粗糙度值的不稳定,且径向振动对表面粗糙度的影响要明显大于其它方向的振动影响。根据现代切削振动信号的测试理论,自制了实验设备,采用压电式加速度传感器提取出不同数控精车工况下与表面粗糙度值存在相关联系的加速度幅值信号,经过自编虚拟仪器软件的后续处理后,输入到具有较强非线性映射能力且经过事先训练的人工神经网络中,进行表面粗糙度值的预测。实验结果表明,经事先训练的人工神经网络对不同工况下的表面粗糙度的预测值与实测值非常接近,这为切削过程中表面粗糙度的在线检测提供了一种新的方法。结合正在开发的具有切削参数自动调整功能的表面粗糙度值的数控系统,可实现切削过程中表面粗糙度的稳定控制,从而在兼顾效率的同时可保证加工的表面质量满足要求。
论文目录
摘要Abstract第一章 绪论1.1 表面粗糙度预测的意义1.2 表面粗糙度在线预测技术概况1.3 论文主要内容第二章 数控加工技术概况2.1 数控加工技术的历史与发展2.1.1 数控技术的发展历史2.1.2 数控机床发展趋势2.2 数控加工技术的基本原理2.3 本章小结第三章 表面粗糙度的形成机理与影响因素3.1 加工表面的成形过程3.2 影响表面粗糙度的因素3.3 表面粗糙度值的评价体系3.3.1 图形表征3.3.2 参数表征3.3.3 分形表征3.4 本章小结第四章 切削振动对表面粗糙度的影响机理4.1 车削中的振动形式4.2 车削振动系统模型分析4.2.1 单自由度系统的振动特性4.2.2 多自由度系统的振动特性4.3 振动模型的建立4.4 振动激励下的表面形状4.5 本章小结第五章 人工神经网络的应用5.1 人工神经网络概述5.1.1 人工神经网络的起源与发展5.1.2 人工神经网络的特点5.2 人工神经网络的结构5.2.1 神经元及其特性5.2.2 人工神经网络的结构5.3 BP网络5.3.1 BP网络模型特点5.3.2 BP网络学习算法5.4 网络的设计5.5 本章小结第六章 实验原理与实验结果6.1 传感器的选择6.1.1 振动位移测量传感器的类型与特点6.1.2 压电式加速度传感器的工作原理6.1.3 传感器的选定6.1.4 传感器的安装6.2 信号采样6.3 信号处理6.4 预测用神经网络的构建6.5 实验方案6.6 神经网络的预测结果图结论与展望参考文献致谢
相关论文文献
标签:神经网络论文; 数控车削论文; 表面粗糙度论文; 在线预测论文; 切削参数论文;
基于神经网络的数控车削过程中零件表面粗糙度的在线预测
下载Doc文档