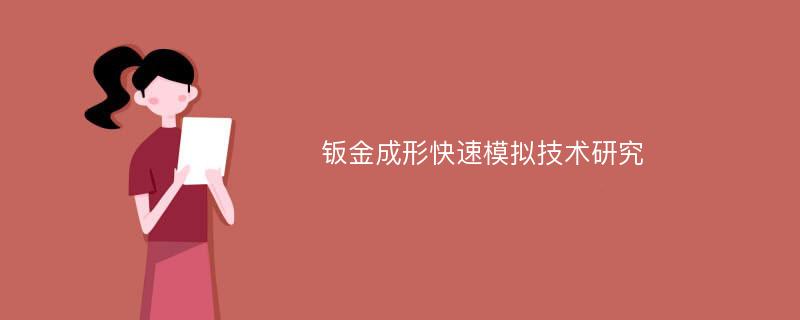
论文摘要
随着计算机技术的发展、数值计算方法的成熟和计算机图形软件的发展,钣金零件成形普遍采用数值模拟方法分析成形过程变化。其中几何模拟法具有初始条件简单、运算效率高、运算成本低的优点,特别是在5%~30%产品详细设计阶段的工艺评审中,能依据简单的工况假设和几何模型,快速简便地定性评价零件的成形可行性。但由于简化了材料性质及其变形流动影响,不计板料各部分在变形中的相互影响,简化了各种外部条件对变形的作用,因而与力学方法相比功能与精度较差。本文主要通过试验确定材料在厚向上的变化来为修正面积的展开提供依据,提高几何模拟法计算精度。 拉深是一种重要冲压成形工艺,在汽车、航空航天、家用电器制造等工业部门以及日常生活用品的冲压生产中,拉深工艺占据相当重要的地位。本文阐述了拉深成形理论,对拉深成形过程进行深入探讨。本文以典型筒形件的拉深成形为对象研究壁厚的变化规律,从而为在体积不变条件下修正面积的展开提供依据。 在理论研究基础上,设计了LY12铝合金带凸缘筒形件拉深成形试验,有针对性地研究了模具凸模相对圆角半径、凹模相对圆角半径两个几何因素对壁厚最大变薄率的影响,得到了两个因素对壁厚最大变薄率影响的主次顺序,及其相应回归模型,获得了多因素壁厚最大变薄率的计算公式,为厚向修正的几何模拟法提供了依据。 最后结合算例分析,给出了拉深成形中壁厚最大变薄率计算公式,并验证了公式的正确性和有效性。
论文目录
摘要ABSTRACT目录第一章 绪论1.1 研究背景及意义1.2 国内外研究现状1.2.1 几何模拟法的技术现状1.2.2 厚度变化研究现状1.3 论文研究内容和章节安排1.3.1 主要研究内容1.3.2 章节安排1.4 本章小结第二章 拉深成形理论2.1 前言2.2 拉深成形理论2.2.1 圆筒件的拉深变形过程2.2.2 圆筒件的拉深变形的力学分析2.2.3 带法兰筒形件的拉深特点2.3 筒形件拉深变形厚度影响因素分析2.3.1 材料力学性能对壁厚的影响2.3.2 凸模圆角半径对壁厚的影响2.3.3 凹模圆角半径对壁厚的影响2.3.4 模具间隙对壁厚的影响2.3.5 压边力对壁厚的影响2.3.6 摩擦对壁厚的影响2.4 本章小节第三章 试验方案设计3.1 试验方案设计3.1.1 试验设计概念3.1.2 试验方法简介3.2 试验准备3.2.1 试验材料3.2.2 试验试件3.2.3 试验仪器与设备3.3 试验过程3.3.1 准备3.3.2 加载3.3.3 卸载3.3.4 数据测量3.3.5 数据处理3.4 本章小结第四章 拉深壁厚变化影响因素分析4.1 回归算法与模型检验4.1.1 一元线性回归算法4.1.2 多元线性回归算法4.1.3 F检验4.2 试验结果及分析4.2.1 试验结果4.2.2 极差分析4.2.3 确定因素的主次顺序4.3 成形参数对壁厚的影响4.3.1 凹模相对圆角半径的回归模型4.3.2 凸模相对圆角半径的回归模型4.3.3 最大变薄率模型4.4 壁厚最大变薄率的验证4.5 本章小结第五章 总结与展望5.1 总结5.2 展望参考文献研究生期间发表论文情况致谢
相关论文文献
标签:几何模拟论文; 拉深成形论文; 厚度变薄率论文; 线性回归论文;