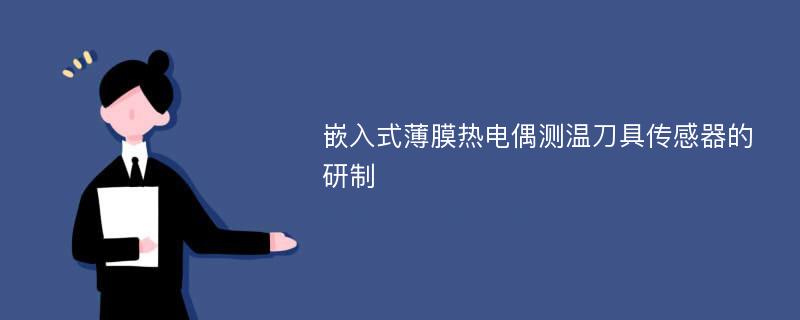
论文摘要
本课题属于切削温度测试研究领域,课题来源于辽宁省自然科学基金项目,项目编号(20062143)和辽宁省教育厅高校科技计划,项目编号(05L023)。本文主要研究瞬态测温传感器——嵌入式薄膜热电偶测温刀具传感器的研制及其性能研究。切削温度直接影响工件的热变形、已加工表面质量、刀具前刀面积屑瘤的产生和消退以及刀具寿命等众多因素,因而现代制造业对切削温度的监测要求逐步提高。铝合金高速切削过程中产生大量的切削热,由于切削速度高,切削热来不及传给工件就被高速流出的切屑带走,工件和刀具累积热量极少。切削热主要集中于刀尖处,而切削区域埋藏于工件内,处于半封闭状态,目前常用的测温方法无法测量刀尖处的切削温度,只能测量距离刀尖一定距离的平均温度。本文研制出一种嵌入式复合薄膜热电偶刀具温度传感器,该传感器集切削、测温为一体,可以快速并精确地测量刀具刀尖处的切削温度。论文的主要内容包括:薄膜热电偶测温传感器的结构优化设计,磁控溅射方法制备SiO2绝缘膜、热电偶薄膜电极,测温传感器的静态标定、动态标定及切削温度测量试验,薄膜热电偶磨损误差分析等。其中,SiO2绝缘膜、薄膜电极的制备以及薄膜热电偶磨损误差分析是本论文工作的重点。通过增加磁控溅射射频偏压的方法,使薄膜热电偶与基体之间的结合力得到改善。采用数控线切割慢走丝加工掩模,使其形状规则、热变形量小。磁控溅射得到的热电偶薄膜膜层致密均匀、平整光滑、边界清晰、在热电极尺寸缩小70%的情况下仍能保证连续。对热电偶进行静态标定和动态标定,得出薄膜热电偶的灵敏度为66.9μV/℃,线性误差不大于0.45%。通过采用两种激光器作为激励热源,分别得到一阶系统的阶跃响应和脉冲响应,热电偶响应时间接近0.25ms。分别制作热接点宽度为1.0mm,0.8mm,0.5mm,0.3mm的热电偶来模拟热电偶磨损过程,实验结果证明热接点宽度从1.0mm~0.3mm对静态和动态数据影响不大,说明热电偶的磨损不会影响其精度和响应时间。
论文目录
摘要Abstract1 绪论1.1 论文选题背景及其研究意义1.2 国内外主要切削温度测试技术介绍1.2.1 自然热电偶法1.2.2 人工热电偶法1.2.3 远红外辐射测温法1.2.4 薄膜热电偶法1.3 溅射薄膜沉积技术简介1.3.1 直流磁控溅射法1.3.2 射频溅射法1.3.3 空阴极放电离子镀1.3.4 多弧离子镀1.3.5 微波ECR等离子体源增强溅射1.4 本文研究的主要内容及组织结构2 嵌入式薄膜热电偶传感器的研制2.1 YG6X测温刀头结构设计与制作2绝缘膜的溅射沉积'>2.2 SiO2绝缘膜的溅射沉积2绝缘膜'>2.2.1 双放电腔MW-ECR射频反应磁控溅射沉积SiO2绝缘膜2.2.2 双放电腔MW-ECR射频反应非平衡磁控溅射原理2.2.3 磁控溅射靶放电特性2.2.4 二氧化硅膜溅射沉积过程及工艺条件2.2.5 二氧化硅膜电性能分析2.2.6 二氧化硅膜附着力测试2.2.7 二氧化硅薄膜膜厚测试2.3 薄膜热电偶的制作2.3.1 热电偶的工作原理2.3.2 薄膜热电偶制作的要求2.3.3 薄膜热电偶的制作2.4 保护层的制作2.5 传感器的装配2.6 本章小结3 嵌入式薄膜热电偶传感器的静动态标定3.1 薄膜热电偶的静态标定3.1.1 薄膜热电偶静态标定注意事项3.1.2 静态标定设备3.1.3 石英晶片上的薄膜热电偶的标定3.1.4 温度自动标定系统3.1.5 系统各部分介绍3.1.6 薄膜热电偶静态标定3.2 薄膜热电偶的动态标定3.3 本章小结4 薄膜热电偶磨损性能研究4.1 薄膜热电偶性能的理论分析4.1.1 薄膜热电偶热电势率4.1.2 薄膜热电偶动态特性理论分析4.2 制作薄膜阵列模拟薄膜磨损过程4.3 薄膜热电偶磨损对静态精度的影响4.4 薄膜热电偶磨损对动态响应的影响5 铝合金切削试验5.1 试验条件5.2 试验结果结论参考文献附录A 附录内容名称附录B 刀具装配图攻读硕士学位期间发表学术论文情况申报专利情况致谢
相关论文文献
标签:切削温度论文; 薄膜热电偶论文; 磁控溅射论文; 激光标定论文; 铝合金切削实验论文;