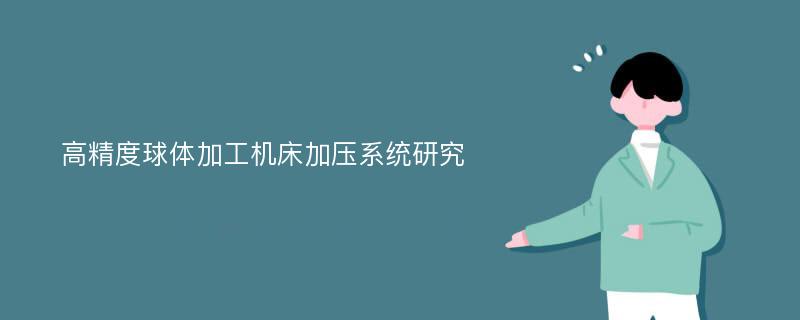
论文摘要
高精度球体是制造高精度轴承的关键零部件之一,广泛应用于精密机床设备和检测设备中。加工载荷是球体加工中最重要的加工参数之一,对球体表面质量和球形误差等有着重要影响,而传统球体加工机床加压系统普遍采用液压加压系统,无法实现载荷的精确控制,对最终成球质量造成一定影响。为解决传统机床加压系统无法精确控制载荷的问题,本文提出了一种新型机械加压系统,采用两组弹簧分段加压的方式实现了载荷的精确控制:并进一步分析其加压误差来源,优化结构设计,使其满足理论所需的加压精度要求。为确定加压系统对加压精度的需求,通过建立双自转研磨方式下球体运动学、力学模型,得到球体做无打滑研磨运动条件下单球所需的最小载荷公式,并测试了油基条件下球体表面摩擦磨损特性,分析得到加压系统所需的加压精度为0.86%FS(满量程百分比)。为满足加压系统加压精度需求,开发了一套采用步进电机驱动,两组弹簧分段加压的新型机械加压系统;并通过建立新型加压系统力学模型并结合测量结果,对加压系统误差来源进行了分析,发现静摩擦力引起的误差是加压精度误差的主要来源,球体振动引起的误差是加工前期控制精度误差的主要来源。针对所分析的误差来源,对加压系统进行了两个方面的改进,主要包括上磨盘调平和弹簧组优化;并对优化弹簧组进行静力学与动力学仿真分析,分析表明,在弹簧组个数为6个,安装半径为180mm的条件下,加压系统的加压均匀性与稳定性最好;改进后加压系统的加压精度达到0.67%F·S,满足加压系统加压精度要求。为验证改进后加压系统的加压性能,在采用更低单球载荷的条件下,对G10级的氮化硅陶瓷球进行了研磨加工实验。实验结果表明,G5级球成球率达到93%,G3级球成球率达到72.5%,且质量优于采用传统加压系统所生产的陶瓷球。
论文目录
摘要ABSTRACT第1章 绪论1.1 课程研究背景1.2 国内外高精度球体加工机床研究现状1.2.1 高精度球体研磨技术的研究1.2.2 国内外主要高精度球体加工机床简介1.2.3 加工载荷对球体加工过程影响的研究1.2.4 高精度球体加工机床加压系统的研究1.3 课题的研究目的与意义1.4 论文结构安排第2章 加压系统加压精度需求分析2.1 球体动力学分析2.1.1 双自转研磨技术运动学分析2.1.2 双自转研磨技术球体力学分析2.2 加压系统加压精度需求分析2.3 球体摩擦磨损实验2.3.1 实验设计2.3.2 实验设备和材料2.3.3 实验条件2.3.4 单因素实验分析2.3.5 摩擦磨损分析2.3.6 实验结论2.4 加压精度计算2.5 本章小结第3章 新型加压系统以及加压误差来源分析3.1 新型加压系统3.1.1 加压系统组成及工作原理3.1.2 加压系统加压性能测试3.2 加压系统力学分析3.3 加压系统加压精度误差影响因素分析3.3.1 压力算法的影响3.3.2 静摩擦力的影响3.3.3 压力传感器精度的影响3.4 加压系统压力控制精度影响因素分析3.4.1 弹簧中径变化的影响3.4.2 加压系统进给精度的影响3.4.3 球体振动的影响3.5 本章小结第4章 加压系统改进4.1 加压系统加压精度误差改进4.1.1 传统V形槽式球体加工机床上磨盘重心位置的理论计算4.1.2 传统V形槽式机床加压系统上磨盘调平方法4.2 加压系统弹控制精度误差改进4.2.1 加压系统弹簧组优化计算4.2.2 优化弹簧组有限元分析4.2.3 优化弹簧组动力学分析4.2.4 弹簧组优选结论4.3 改进后加压系统加压精度测量4.4 本章小结第5章 高精度氮化硅陶瓷球加工实验5.1 高精度球体加工机床研磨加工实验5.1.1 实验条件5.1.2 实验过程5.2 实验结果及讨论5.2.1 球形偏差变化分析5.2.2 陶瓷球表面质量分析5.2.3 不同阶段去除率分析5.2.4 振动值对比分析5.2.5 成球精度统计5.3 本章小结第6章 总结与展望6.1 课题总结6.2 课题展望符号说明参考文献致谢攻读学位期间参加的科研项目和成果
相关论文文献
标签:高精度球体加工机床论文;