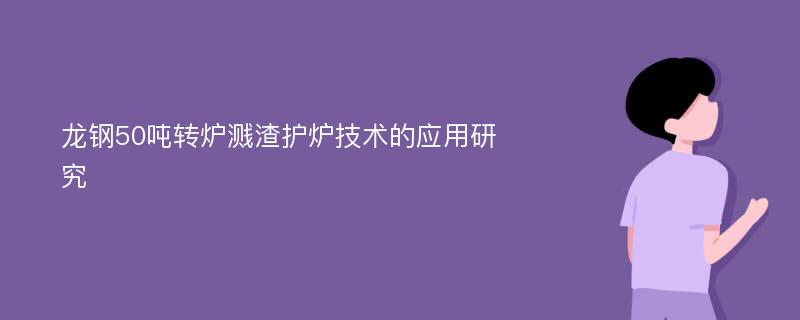
论文摘要
转炉溅渣护炉技术是近十几年来转炉炉衬维护技术的一项重大突破,国内外许多钢厂开发研究并应用该项技术,使转炉炉龄大幅度提高,同时取得了明显的经济效益。龙钢从1997年开始在15t转炉上采用溅渣护炉技术,使转炉炉龄由1000多炉提高到3000多炉。目前,龙钢在50t转炉也采用了溅渣护炉技术,但是与国内外先进水平相比尚存在较大差距,因此对龙钢溅渣护炉技术进行深入研究具有重要的工程价值和理论意义。本课题结合龙钢现状,通过对龙钢50t转炉溅渣护炉工艺制度、物料结构进行调整,同时对生成渣的渣相、熔化性能、熔化温度及炉衬的结合机理进行研究,得到如下主要结论:(1)通过理论分析及生产实践证实:龙钢适宜的溅渣工艺参数为:枪位0.8-2.2m,渣量2.5-3.5t,吹氮压力为0.9-1.6MPa,气体流量为8000-10000Nm3/h,溅渣时间2-3min;(2)采用溅渣护炉工艺,耐火材料用量明显减少、成本显著下降。耐材成本降低了3.8元/吨钢,转炉平均炉龄达到12000炉,最高炉龄达到21129炉;(3)炉渣碱度、∑FeO和MgO含量是影响终点炉渣耐火度的主要因素。要使溅渣层有足够的耐火度,主要措施是调整渣中MgO含量,终渣MgO含量控制在8%~12%、碱度R值控制在3.0~3.5范围,∑FeO控制在10%~15%;(4)降低炉渣过热度,使炉渣熔点和粘度提高,有利于提高溅渣层的耐蚀性、抗冲刷性能及改善炉渣与炉衬之间的粘附作用。炉渣熔点和粘度的提高,加上改质剂对炉渣的快速降温作用,可以缩短溅渣孕育时间,也可以抑制炉衬中石墨被炉渣氧化,气隙消失,使炉渣与炉衬粘结更好。
论文目录
摘要ABSTRACT1 绪论1.1 前言1.2 国外溅渣护炉技术回顾1.2.1 发展及现状1.2.2 溅渣护炉方法1.2.3 物理模型1.2.4 溅渣设备1.3 我国溅渣护炉的发展及现状1.3.1 应用溅渣护炉技术的必要性1.3.2 应用溅渣护炉技术的基本条件1.4 本课题研究的目的及意义1.5 本课题的主要研究内容和技术方案1.5.1 主要研究内容1.5.2 研究方案2 溅渣护炉理论及实际应用分析研究2.1 溅渣护炉机理2.1.1 溅渣枪位对溅渣量的影响2.1.2 气体滞止压力(或流量)对溅渣的影响2.1.3 渣池留渣量对溅渣的影响2.1.4 喷孔分布及喷孔夹角对溅渣的影响2.1.5 熔渣粘度对转炉溅渣的影响2.2 溅渣层与炉衬结合机理研究2.2.1 溅渣层与炉衬结合机理2.2.2 龙钢转炉溅渣层与炉衬结合机理实验2.2.3 实验结果及讨论2.2.4 讨论分析2.3 转炉溅渣护炉的工艺制度2.3.1 转炉溅渣护炉的特点2.3.2 转炉溅渣护炉操作流程2.3.3 转炉溅渣护炉工艺操作参数2.3.4 溅渣护炉的氮气压力、供气强度的确定2.3.5 溅渣时间2.3.6 渣中氧化镁含量2.3.7 溅渣护炉的渣量2.3.8 调渣剂2.3.9 吹炼过程中提高炉渣中MgO含量2.3.10 终渣的调整2.3.11 氮气喷吹参数2.3.12 复吹转炉的溅渣操作2.4 溅渣护炉配套技术2.4.1 加强设备维护2.4.2 进一步提高转炉炉龄2.4.3 完善供氮系统2.4.4 深入研究溅渣护炉工艺2.4.5 开发炼钢厂设备运行保障技术2.5 溅渣护炉技术存在的问题和发展前景2.5.1 存在的问题2.5.2 溅渣护炉技术在我国的发展前景2.6 小结3 龙钢溅渣护炉工艺工业试验3.1 龙钢炼钢厂转炉生产基本情况3.2 溅渣护炉试验3.2.1 调渣剂3.2.2 改质剂3.3 造渣工艺的调整3.4 炉渣性能研究3.4.1 溅渣护炉试验前、后炉渣化学成分分析3.4.2 炉渣中MgO含量(wt)3.4.3 炉渣TFe含量3.4.4 炉渣中w(FeO)3.4.5 炉渣碱度3.5 试验前、后炉渣熔化性能的分析3.5.1 试验前炉渣始熔温度、熔化温度与熔毕温度3.5.2 溅渣试验炉渣的始熔温度、熔化性温度与熔毕温度3.6 造渣制度3.7 溅渣吹氮工艺制度3.8 龙钢转炉溅渣护炉技术优化结果与分析3.8.1 控制合理的留渣量3.8.2 溅渣枪位的控制3.8.3 溅渣时间的控制3.8.4 调渣剂的合理利用3.8.5 转炉出钢温度3.8.6 终渣的改善3.8.7 炉型控制3.8.8 供氧制度的优化3.8.9 渣料结构的优化3.8.10 强化过程控制3.8.11 加强生产管理3.8.12 溅渣与补炉的配合3.9 龙钢溅渣护炉存在的问题及进一步改进的方向3.9.1 龙钢转炉溅渣护炉存在的问题3.9.2 展望3.10 本章小结4 结论致谢参考文献
相关论文文献
标签:转炉论文; 炉龄论文; 溅渣护炉论文; 工艺参数论文; 炉渣特性论文;