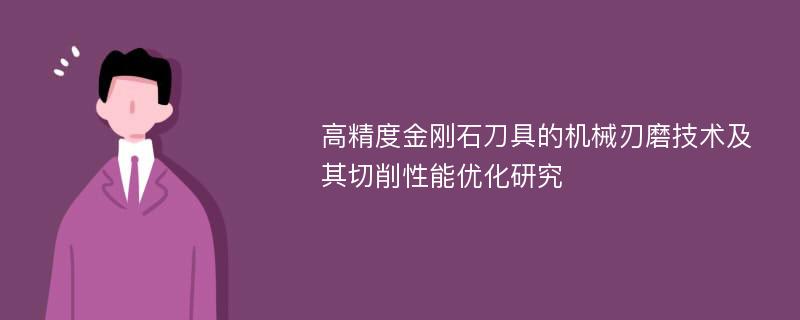
论文摘要
随着超精密切削加工技术的应用与推广,超精密切削的加工精度逐渐向纳米尺度及其极限精度发展。在超精密切削加工中,为了使加工零件获得纳米、亚纳米特征的加工精度,除了需要超精密的车床、高分辨率的检测仪器和超稳定的加工环境外,高精度的金刚石刀具是必须具备的条件,尤其是圆弧刃金刚石刀具。机械刃磨技术以设备低廉、工艺简单等优点,成了目前金刚石刀具制备行业最常用的技术。但现阶段的机械刃磨技术只能加工出切削刃钝圆半径(切削刃钝圆半径亦称锋利度)为7080nm的金刚石刀具,该指标已远远不能满足当前超精密切削加工技术发展的需求,在某种程度上却成了超精密切削加工技术发展的制约瓶颈。因此,如何突破这一技术瓶颈以获取小于50nm甚至更锋利切削刃钝圆半径的廉价金刚石刀具成了现阶段超精密切削加工技术发展亟需解决的问题。本论文围绕高精度圆弧刃金刚石刀具的机械刃磨工艺,先从加工机理入手,提出了金刚石晶体材料的脆塑转变机械研磨机理,建立了具有各向异性特征的金刚石晶体材料去除方式的动态脆塑转变临界研磨深度的理论计算模型。根据脆塑转变研磨理论,本文对金刚石晶体易磨和难磨方向表层材料的不同研磨去除机理进行了统一解释,并对金刚石晶体研磨效率的各向异性进行了量化比较。根据理论推导的动态脆塑转变临界研磨深度,本文深入分析了各刃磨工艺参数对刀具切削刃钝圆半径刃磨质量的影响,建立了可稳定获取3055nm切削刃钝圆半径的机械刃磨工艺。此外,本文采用时间序列分析方法,构建了金刚石刀具切削刃钝圆半径随刃磨时间变化的指数与自回归耦合时间序列预测模型,由此可根据切削刃钝圆半径的具体刃磨要求确定刀具刃磨时间,减少了不必要的重磨或过磨及昂贵的刃口检测,提高了生产效率,降低了生产成本。根据脆塑转变机械研磨理论,本文又从理论上推导出了金刚石晶体的动态微观机械强度,包括动态微观抗拉、抗压和剪切强度,通过对比分析金刚石晶体难易磨方向的动态微观机械强度,探索出了金刚石刀具要获取最锋利的刀具刃口需以金刚石晶体易磨方向的动态微观抗拉强度作为前后刀面的设计准则,而金刚石刀具要获取最佳抗磨损性能则需以金刚石晶体难磨方向的动态微观抗拉强度作为前后刀面的设计准则。基于金刚石晶体的动态微观机械强度,本文通过分析刀具刃口的受力情况,从理论上推导出了金刚石刀具的刃口极限锋利度,即(110)晶面作前刀面时可以达到16nm,而(100)晶面作前刀面时则可达25nm。根据理论推导的假设条件,开发出了新型的热-机耦合刃磨工艺。刃磨实验结果表明,前后刀面分别定向为(110)和(100)晶面的金刚石刀具经过新工艺处理可获取29nm的切削刃钝圆半径,实验数据与理论值很好的吻合。另外,本文经过对单晶硅进行大量的超精密切削实验,发现了金刚石刀具发生急剧磨损的主要原因是刀具后刀面的沟槽磨损。进一步的研究又表明,沟槽磨损的产生则是由于碳化硅和类金刚石超硬微颗粒形成后在金刚石刀具后刀面发生刻划和耕犁所导致。最后,本文基于有限元仿真技术和通用旋转组合实验设计方法,建立了高导无氧铜超精密切削的已加工表面残余拉应力和残余压应力对刀具几何参数的二次回归数学模型,由此通过分析刀具几何参数对残余应力的影响,优选出了适于塑性材料超精密切削加工的金刚石刀具几何参数,即在切削刃钝圆半径100300nm、切削速度210m/s、前角-15°15°和后角2°10°的取值范围内,刀具的优化参数为:前角5°,后角10°,刀具切削刃钝圆半径则越小越好。
论文目录
摘要Abstract第1章 绪论1.1 课题的背景和来源及研究的目的和意义1.2 国内外金刚石刀具刃磨技术水平的对比1.2.1 国外的金刚石刀具刃磨技术水平1.2.2 国内的金刚石刀具刃磨技术水平1.3 金刚石刀具刃磨关键技术的国内外发展概况1.3.1 金刚石刀具晶体的定向技术1.3.2 金刚石刀具的刃磨工艺方法1.3.3 金刚石刀具的刃口检测方法1.3.4 金刚石晶体的机械研磨机理研究1.4 金刚石刀具切削性能优化技术的国内外发展概况1.4.1 金刚石刀具几何参数的有限元优化技术1.4.2 金刚石刀具急剧磨损的抑制技术1.5 本课题的主要研究内容第2章 金刚石晶体的机械研磨机理2.1 金刚石晶体的物理和化学及力学特性2.1.1 金刚石晶体的结构和分类2.1.2 金刚石晶体的密度和石墨化条件及化学稳定性2.1.3 金刚石晶体的弹性特征和各向异性2.1.4 金刚石晶体的力学特性2.2 金刚石晶体脆塑转变机械研磨机理的提出2.3 金刚石晶体脆塑转变临界研磨深度的实验验证2.3.1 实验设备及实验条件2.3.2 [100]晶向和[110]晶向的微观形貌比较2.3.3 最大塑性沟槽深度与理论临界值的比较2.3.4 研磨效率各向异性的量化比较2.4 金刚石晶体机械研磨的碎屑相变问题2.5 脆塑转变研磨机理在金刚石刀具刃磨中的利用2.6 本章小结第3章 高精度金刚石刀具的机械刃磨工艺3.1 表面粗糙度相关工艺参数对切削刃钝圆半径的影响3.1.1 刀体夹具的往复运动3.1.2 金刚石磨粒尺寸3.2 接触精度相关工艺参数对切削刃钝圆半径的影响3.2.1 刃磨机床振动3.2.2 主轴动平衡精度3.2.3 研磨盘表面研磨质量3.2.4 研磨速度3.2.5 研磨压力3.3 刃磨工艺参数的优化组合3.4 前后刀面定向对切削刃钝圆半径的影响3.5 时间序列法分析切削刃钝圆半径的变化规律3.5.1 实验条件及切削刃钝圆半径的原始测量数据3.5.2 时间序列分析与预测模型的建立3.5.3 切削刃钝圆半径时间序列预测模型的应用3.6 本章小结第4章 金刚石刀具的极限锋利度4.1 金刚石晶体动态微观机械强度的理论推导4.2 金刚石刀具极限锋利度的理论预测4.2.1 前刀面为(110)晶面的刀具极限锋利度4.2.2 前刀面为(100)晶面的刀具极限锋利度4.3 金刚石刀具极限锋利度的实验验证4.3.1 实验条件4.3.2 刃磨工艺参数的影响4.3.3 金刚石刀具极限锋利度的实现4.4 本章小结第5章 金刚石刀具的抗磨损性能优化5.1 金刚石刀具抗磨损性能研究的实验条件5.1.1 金刚石刀具和工件材料5.1.2 超精密切削机床5.1.3 切削参数的选择5.1.4 评价参数及相关检测设备5.2 金刚石刀具抗磨损性能的理论预测5.3 金刚石刀具抗磨损性能的实验验证5.3.1 金刚石刀具急剧磨损的实验分析5.3.2 金刚石刀具磨损量的各参数评价5.4 本章小结第6章 金刚石刀具几何参数的有限元优化6.1 有限元模型的建立和边界条件的设定6.1.1 有限元网格的划分6.1.2 工件材料的建模6.1.3 切屑的形成6.1.4 切削热的计算6.1.5 摩擦模型6.2 超精密切削的加载和卸载及散热过程模拟6.3 有限元仿真实验的通用旋转组合设计6.4 回归方程预测数据可靠性的实验验证6.5 已加工表面残余应力的影响因素分析6.5.1 切削刃钝圆半径6.5.2 切削速度6.5.3 刀具后角6.5.4 刀具前角6.5.5 金刚石刀具几何参数的优化6.6 本章小结结论参考文献附录攻读博士学位期间发表的论文致谢个人简历
相关论文文献
标签:高精度金刚石刀具论文; 机械研磨机理论文; 设计准则论文; 极限锋利度论文; 抗磨损性能论文;
高精度金刚石刀具的机械刃磨技术及其切削性能优化研究
下载Doc文档