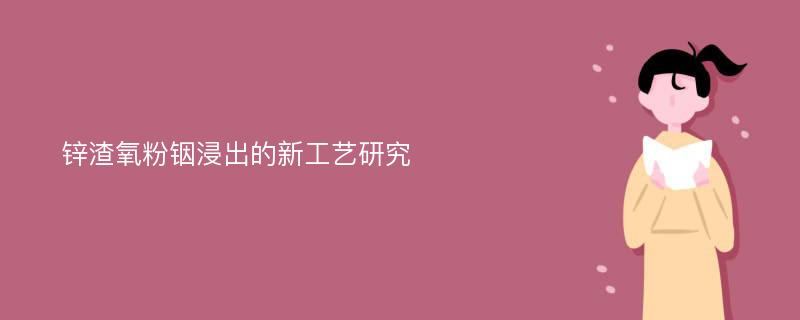
论文摘要
本文综述了铟、锌渣氧粉以及机械活化、加压氧化工艺在湿法冶金浸出应用上的情况,研究采用机械活化(边活化边反应)和加压氧化两种方法强化锌渣氧粉浸铟的工艺,得出不同工艺条件下锌渣氧粉在工业硫酸体系中浸铟的规律,以及浸铟的较优工艺条件。实验结论如下:(1)锌渣氧粉通过机械活化或者加压氧化工艺浸铟时,都可缩短浸出时间,强化浸出过程,为贫铟物料的铟浸出开辟了两条新的工艺路线。在搅拌磨活化正交试验中,各因素对铟浸出率的影响程度为:硫酸初始浓度>搅拌转速>反应时间>液固比。(2)综合各方面因素,用搅拌磨活化装置浸铟时,在实验范围内最佳工艺条件为:活化反应时间为150 min、液固比为8、酸初始浓度为5 mol/L、搅拌速度为575 r/min。此时,铟浸出率可由常规自热浸出时的68.1%提高到91.2%。(3)在双氧水加压氧化浸铟时,实验范围内最佳工艺条件为:液固比为8、反应时间为150 min、搅拌速度为575 r/min、反应温度为90℃、釜内压力为0.5 MPa(空气加压)、硫酸初始浓度为5 mol/L、双氧水(H2O2含量为30%)用量为0.5 mL/g矿。此时,铟浸出率可由常规恒温90℃(无氧化剂)浸出时的77.6%提高到90.2%。在高锰酸钾加压氧化浸铟时,实验范围内最佳工艺条件为:液固比为8,反应时间为150 min,搅拌速度为575 r/min,反应温度为90℃,釜内压力为0.5 MPa(空气加压),硫酸初始浓度为3 mol/L,高锰酸钾用量为25 g/kg矿。此时,铟浸出率可由常规恒温90℃(无氧化剂,硫酸初始浓度为5 mol/L)浸出时的77.6%提高到89.5%。(4)在酸初始浓度较低时,氧化剂的加入使氧化浸出效果优于机械活化的效果。高锰酸钾加压氧化浸出能在较低硫酸初始浓度下达到较高的铟浸出率,且在硫酸初始浓度较高时,高锰酸钾加压氧化浸出仍然具有较大的优势。
论文目录
摘要ABSTRACT符号说明前言第一章 铟提取技术的研究进展1.1 铟的概况1.1.1 铟的性质和用途1.1.2 铟资源的分布情况1.1.3 铟的提取方法1.1.4 铟的微量分析方法1.2 锌渣氧粉及其处理工艺1.3 机械活化的概述1.3.1 机械活化的原理1.3.2 机械活化的设备1.3.3 机械活化在浸出过程中的应用1.4 铟的其它强化浸出工艺1.4.1 强化浸铟的主要工艺1.4.2 加压氧化浸出工艺1.5 研究设想及意义第二章 锌渣氧粉在硫酸体系中浸铟的理论基础2.1 矿物浸出过程2.2 锌渣氧粉浸铟反应的热力学分析2.3 锌渣氧粉浸铟反应的动力学分析第三章 机械活化强化锌渣氧粉浸铟的工艺研究3.1 研究的主要内容3.2 实验原料3.3 实验设备3.4 实验方案设计3.5 实验操作3.5.1 机械活化过程3.5.2 常规浸出过程3.6 结果分析及讨论3.6.1 正交试验结果分析3.6.2 常规恒温搅拌浸出时温度对铟浸出率的影响3.6.3 搅拌转速对铟浸出率的影响3.6.4 酸初始浓度对铟浸出率的影响3.6.5 液固比对铟浸出率的影响3.6.6 活化反应时间对铟浸出率的影响3.6.7 不同浸出工艺方法的浸铟效果比较3.7 小结第四章 加压氧化强化锌渣氧粉浸铟的工艺研究4.1 研究的主要内容4.2 实验原料4.3 实验设备4.4 实验方案设计4.5 实验操作4.5.1 加压氧化浸出过程4.5.2 常规氧化浸出过程4.6 结果分析及讨论4.6.1 氧化剂用量对铟浸出率的影响4.6.2 酸初始浓度对铟浸出率的影响4.6.3 加压氧化与常压氧化的浸铟效果比较4.6.4 氧化剂种类对铟浸出率的影响4.6.5 不同浸出工艺方法浸铟效果的比较4.7 小结第五章 结论与展望5.1 结论5.2 展望参考文献附录附录1 铟标准溶液的配置方法附录2 溶液铟含量的极谱分析方法附录3 铟浸出率的计算附录4 实验数据致谢攻读学位期间发表论文情况
相关论文文献
标签:锌渣氧粉论文; 机械活化论文; 加压氧化论文; 浸出论文;