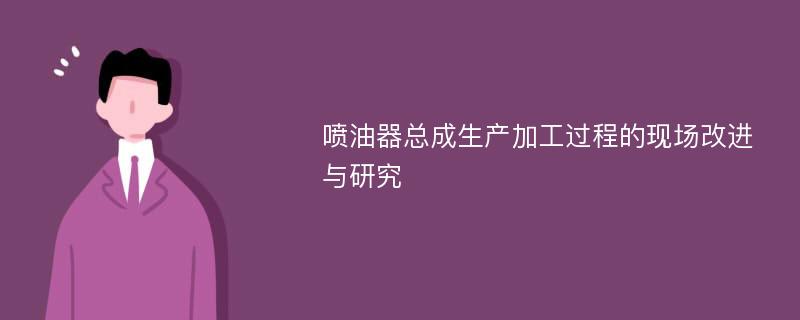
论文摘要
本文是对持续改进的相关理论在喷油器总成生产现场改进的研究与应用。在研究过程中,本文将持续改进理论分为系统持续改进,点改进和现场持续改进等三部分,据此提出改进的模型,研究其在现场的实施与应用。在改善过程中,通过对一次装配合格率和报废的分析,运用帕累多排列图确定主要问题,运用鱼刺图确定主要原因;通过流程图,绘制价值流图,发现生产流程中的浪费。由于生产线是以手工作业为主,在应用工作研究理论中的方法研究和作业测定技术时,采用作业测定理论中的方法时间衡量(MTM)为主要手段,同时也用时间研究(秒表测时法)来进行分析,结合生产线的布局,运用“5W1H”提问技术,对各工位完成任务的目的、方法、人员、时间、地点及原因等方面进行提问,逐项进行分析。同时分析生产线存在的问题,确定生产线的瓶颈工位,识别现场的浪费。在考虑改进方案时,根据持续改进的相关理论,结合生产线平衡理论,对生产线的瓶颈工位进行改善,减少浪费,吸引员工参与改进。同时,结合精益生产的相关理论,并重新布置生产线,建立拉动式的生产方式,提高生产能力。
论文目录
摘要ABSTRACT第一章 绪论1.1 论题的题目来源1.2 论题的产生背景1.2.1 国内外柴油汽车发展情况的趋势要求1.2.2 客户对质量成本及交货的要求1.3 论题研究的现状及研究的意义1.3.1 现场改进在国内企业的应用情况1.3.2 喷油器总成质量对柴油机的影响1.4 论题研究的内容第二章 持续改进及其相关方法和理论2.1 持续改进产生的背景2.1.1 改善与创新的区别2.1.2 丰田生产中的持续改进2.1.3 ISO9000-2000版中的持续改进2.1.4 持续改进的原则2.1.5 持续改进的实质:PDCA循环2.2 常用的改善方法—质量改进的基本方法2.2.1 一般性方法:5W1H 和头脑风暴法2.2.2 QC 七法2.3 精益生产的改进理论与方法2.3.1 精益生产改进理论简介2.3.2 通过价值流分析发现浪费2.4 工业工程改进方法与理论2.4.1 工作研究2.4.2 流程活动图分析法2.4.3 “ECRS”四大原则2.4.4 生产线布局与平衡2.5 持续改进的实施2.6 本章小结第三章 喷油器总成生产加工过程的现状分析3.1 产品及工艺流程介绍3.1.1 喷油器总成产品简介3.1.2 喷油器总成工艺流程分析3.2 问题的提出3.3 公司生产现状3.3.1 生产能力分析3.3.2 一次装配合格率分析3.3.3 价值流分析发现生产中的浪费3.3.4 时间分析发现生产岗位的不平衡3.4 改进的目标及改进的方法3.5 本章小结第四章 喷油器总成改善方案的实施4.1 系统的持续改进4.1.1 工作岗位的时间测定4.1.2 U 型生产线的设计4.1.2.1 分析客户的需求4.1.2.2 确定操作工的操作流程4.1.2.3 设计新的生产线4.1.2.4 模拟新的生产线4.2 点的持续改进4.2.1 标准化工作4.2.2 建立快速响应系4.2.3 有组织的沟通4.2.4 持续的问题解决4.2.5 过程确认4.3 现场持续改进4.3.1 实施 5S 改善现场4.3.2 通过“现场学习”小组活动吸引现场员工参与改进4.3.3 通过合理化建议和问题解决小组来激励员工参与改进4.3.4 不同层次和部门员工通过研讨会共同参与改进4.3.5 生产过程质量控制4.4 实施持续改进效果的维持与启示4.5 本章小结第五章 结论参考文献致谢攻读学位期间发表的论文
相关论文文献
标签:精益生产论文; 系统持续改进论文; 点持续改进论文; 现场持续改进论文;