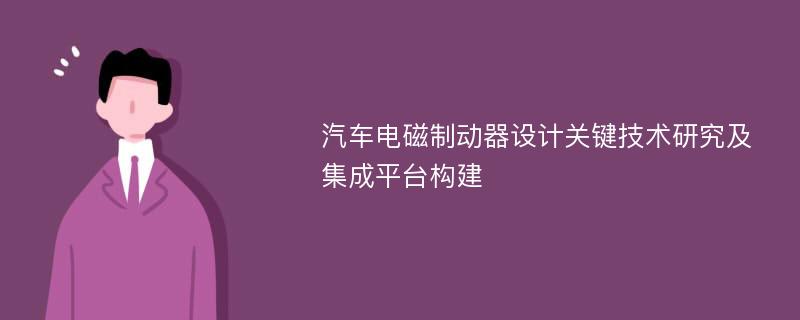
论文摘要
电磁制动器在国外已普遍应用于拖挂式车辆制动系统中,作为关系汽车安全的关键部件之一,其性能的好坏将直接影响汽车整车的安全性能。当前,汽车技术的发展对电磁制动器的设计提出了高性能、低成本和短周期的要求,迫切需要借助计算机辅助设计技术为电磁制动器的设计提供支撑。本文针对电磁制动器设计的关键技术进行研究,以建立电磁制动器集成设计平台为目标,主要开展了以下几个方面的研究内容:对汽车列车制动力匹配技术进行了研究,确定了牵引车和房车的制动力分配系数,依据相关标准运用制动器与整车性能相匹配的理论,建立了房车所需制动力矩的数学模型,用以对制动器进行选型设计,并给出了集成设计平台中整车匹配模块的算法流程图。通过对鼓式电磁制动器力学性能的分析和研究,提出了一种实用的鼓式制动器制动效能因数的计算方法,并给出了相关的计算公式。基于鼓式电磁制动器结构参数对制动效能因数的敏感性分析,以制动效能为优化目标,建立了制动器优化设计数学模型,确定了鼓式电磁制动器优化设计的主要结构参数。通过分析优化设计的约束条件,给出了基于Matlab的Fmincon函数的程序优化算法和实现方法。建立了基于ADAMS的电磁制动器虚拟样机模型,通过试验和仿真,比较优化前后制动器的性能,验证了优化设计方法的有效性及虚拟样机模型的正确性。从研究电磁制动器的工作机理出发,分析了电磁体制动时的工作姿态及其表面磨损的情况,为实现电磁体表面均匀磨损和抗旋转趋势,提出了电磁体的优化设计方案。基于电磁体表面内侧开槽的非对称设计构想,计算了理论开槽面积。利用三维电磁场分析软件Maxwell 3D对非对称结构电磁体进行了仿真分析,以仿真结果对理论分析及设计作出了合理修正,从而得到了最佳的开槽结构。通过将对称结构和自制非对称结构的电磁体做耐久性磨损试验对比,验证了非对称结构电磁体的磨损均匀性明显提高及电磁体优化设计的合理性。通过对稳健优化设计原理与方法的研究,将基于损失模型的稳健设计方法应用于制动器的设计,将影响制动器输出特性的因素划分为可控因素和噪声因素,并应用传统优化思想,确定了各因素的中心值及波动。通过正交试验,计算出试验结果,进行直观分析或方差分析,获取每个因素对试验结果影响的重要程度,最终得出了各因素对产品质量的贡献率;将基于响应面模型的稳健设计方法应用于电磁体的设计,通过试验获得电磁体相关数据,并运用回归的方法建立了响应面模型。将传统的稳健设计方法与现代计算方法相结合,运用Matlab中相关的优化函数,获得了电磁体稳健点以及电磁体所应具有的输出特性。通过分析电磁制动器设计过程及其影响因素,研究并分析了电磁制动器集成设计平台的内涵,提出了基于集成设计平台的电磁制动器设计过程,建立了集成设计平台的运作体系和系统体系,分析了集成设计平台的体系结构特征;通过分析电磁制动器设计过程中的基本数据元素和模型,建立了由组织、过程和产品三个视图组成的多视图集成数据模型,提出了基于数据库的主模型数据一致性管理方法,实现了平台的数据集成;提出了基于组件技术思想建立集成设计平台应用集成的方法,给出了组件形式化定义及集成设计平台中应用组件接口,提出了集成平台中组件的分类方法和原则,给出了组件互操作的实现方案,并详细论述了相关应用软件的集成方法。最后,通过集成设计平台的开发及相关功能模块的建立,验证了研究成果的可行性、有效性和实用性。
论文目录
摘要ABSTRACT第一章 绪论1.1 研究背景及意义1.2 相关问题的国内外研究现状1.2.1 电磁制动器设计关键技术1.2.2 集成设计平台及其关键技术1.3 目前研究中存在的问题1.4 论文的研究内容及组织结构第二章 汽车列车制动力匹配技术研究2.1 拖挂式房车制动力匹配技术的研究2.1.1 牵引车和房车制动力分配系数的确定2.1.2 电磁制动器最小制动力矩的确定2.1.3 电磁制动器最大制动力矩的确定2.2 电磁制动器选型设计在平台中的实现2.3 本章小结第三章 制动器结构参数优化及虚拟样机的建立3.1 制动器因数与制动蹄因数3.1.1 制动蹄摩擦面的径向变形规律及压力分布规律3.1.2 制动器因数的求解思路3.1.3 电磁制动器主领蹄制动效能因数的计算3.1.4 电磁制动器次领蹄制动效能因数的计算3.2 制动器的敏感度3.3 电磁制动器优化设计结构参数的确定3.3.1 包角和起始角的确定3.3.2 摩擦衬片宽度的确定3.3.3 其他参数的确定3.4 电磁制动器结构参数优化模型的建立3.4.1 优化模型约束条件的确定3.4.2 优化工具的选取3.5 基于ADAMS电磁制动器虚拟样机技术的研究3.5.1 电磁制动器虚拟样机建模3.5.2 试验验证3.6 结构参数优化设计在平台中的实现3.7 本章小结第四章 电磁体结构设计研究及优化4.1 电磁体的力学特性分析4.1.1 电磁体结构4.1.2 电磁体与制动鼓之间的接触分析4.2 电磁体非X轴对称设计4.2.1 问题的提出4.2.2 理论分析4.3 电磁体非Y轴对称设计4.3.1 问题的提出4.3.2 理论分析4.4 电磁体仿真分析及磨损实验4.4.1 基于Maxwell 3D的电磁体仿真分析4.4.2 非轴对称电磁体磨损实验4.5 电磁体优化设计在平台中的实现4.6 本章小结第五章 电磁制动器稳健优化设计研究5.1 稳健设计概述5.1.1 稳健优化设计的基本原理5.1.2 稳健优化设计的一般步骤5.1.3 常用稳健设计方法比较5.1.4 相关稳健优化设计方法的选择5.2 基于损失模型的制动器部分稳健优化设计5.2.1 基于损失模型稳健优化设计概述5.2.2 制动器部分稳健优化设计5.3 基于响应面模型的电磁体部分稳健优化设计5.3.1 基于响应面模型稳健优化设计概述5.3.2 电磁体稳健优化设计5.4 稳健优化设计在平台中的实现5.5 本章小结第六章 电磁制动器集成设计平台的构建6.1 集成设计平台的内涵与电磁制动器设计过程分析6.1.1 影响设计质量的主要因素6.1.2 传统机械产品CAD平台面临的主要问题6.1.3 解决方案与集成设计平台的内涵6.1.4 基于集成设计平台的电磁制动器设计过程6.2 电磁制动器集成设计平台体系结构6.2.1 集成设计平台的系统特征6.2.2 集成设计平台的运作体系结构6.2.3 集成设计平台的系统体系结构6.2.4 集成设计平台的系统结构特征6.3 基于多视图集成数据模型的数据集成6.3.1 数据集成方法分析6.3.2 集成设计平台的基本数据模型与视图6.3.3 基于数据库的主模型一致性管理6.4 基于组件技术思想的应用集成6.4.1 组件技术6.4.2 集成设计平台组件分类6.4.3 组件互操作6.4.4 相关应用软件的集成方法6.5 集成设计平台的实现6.5.1 EBVAS虚拟装配模块6.5.2 电磁制动器设计评价模块6.5.3 数据库用户管理6.6 本章小结第七章 结论与展望7.1 本文完成的主要工作7.2 本文的主要创新点7.3 后续工作展望参考文献致谢在读期间发表的学术论文附录1 电磁体稳健优化设计试验数据表附录2 软件测试报告
相关论文文献
标签:电磁制动器论文; 电磁体论文; 集成设计平台论文; 优化设计论文; 稳健设计论文;