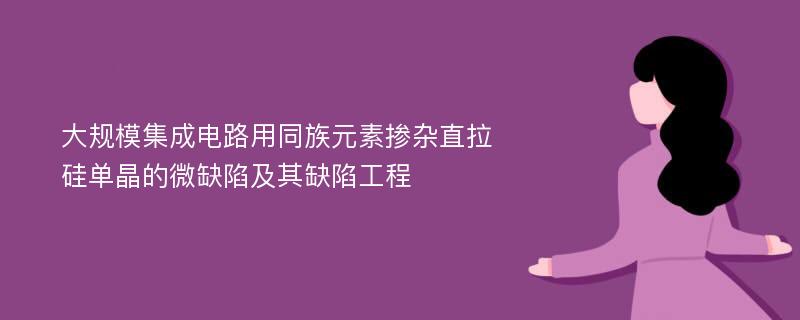
论文摘要
超大规模集成电路的高速发展对硅单晶材料提出了愈来愈严格的要求,控制和消除直拉硅中的微缺陷是硅材料开发面临的最关键的问题。随着直拉硅单晶的大直径化,硅中氧含量有所下降,而当代集成电路以超浅结为特征,其制造工艺的热预算显著降低,这两方面都不利于直拉硅中的氧沉淀,从而削弱了硅片的内吸杂能力,使得传统的内吸杂工艺受到了挑战。另一方面,在大直径直拉硅中形成的空洞型缺陷(Void)若得不到有效的控制,将会影响金属-氧化物-半导体(MOS)器件的栅极氧化层完整性(GOI),从而降低集成电路的成品率。利用共掺杂技术来调控硅中的微缺陷和增强硅片的内吸杂能力是目前硅材料研究的热点,开发新型共掺杂直拉硅单晶具有重要的理论意义和实用价值,是目前和今后国际硅材料界重要的研究领域之一。本文在生长同族元素(锗、碳)掺杂的新型直拉硅单晶的基础上,系统的研究了掺锗直拉(GCZ)硅和高碳含量的直拉(H[C]CZ)硅中的氧沉淀行为以及Void产生和消除的规律,揭示了同族元素杂质影响直拉硅中微缺陷行为的机理;同时,研究了适用于这两种新型直拉硅片的内吸杂工艺,取得了如下所述的创新结果:(1)研究了微量锗杂质影响直拉硅中氧沉淀的规律,发现掺锗可以促进原生氧沉淀的形成并在很宽的温度范围(650-1150℃)内促进后续退火过程中的氧沉淀。揭示了微量锗杂质影响直拉硅中氧沉淀的机理,指出GCZ硅中形成的Ge-V和Ge-V-O等锗关复合体可以作为氧沉淀的异质形核核心,从而促进氧沉淀的形成。同时,发现掺锗能显著降低直拉硅中氧沉淀的高温热稳定性,指出这是由于GCZ硅中形成了小尺寸的氧沉淀和片状氧沉淀所致。(2)研究了基于普通炉退火(CFA)和快速热退火(RTA)处理的适用于GCZ硅片的内吸杂工艺。发现掺锗能促进直拉硅片在高-低-高三步退火过程中的氧沉淀从而提高体微缺陷(BMD)密度并同时减小洁净区(DZ)宽度。通过RTA预退火结合低-高两步退火或高温单步退火的热处理工艺,在GCZ硅片中形成高密度的BMD和宽度合适的DZ,这有助于减小集成电路制作过程中内吸杂工艺的热预算。同时,明确指出:通过上述两种工艺形成的DZ中不存在微小氧沉淀,并且GCZ硅片体内BMD区吸除金属沾污的能力优于普通直拉(CZ)硅片。(3)研究了适用于H[C]CZ硅片的内吸杂工艺及其氧沉淀规律,发现高浓度碳杂质可以在内吸杂工艺过程中促进硅中的氧沉淀。揭示了碳影响氧沉淀的机理,指明H[C]CZ硅中形成的C(3)中心和C-V等碳关复合体会促进氧沉淀的生成。并且通过基于CFA和RTA处理的内吸杂工艺在H[C]CZ硅片中形成了没有微小氧沉淀的DZ和具有比CZ硅片更高密度的BMD。该结果为H[C]CZ硅片在集成电路制造中的可能应用提供了理论依据。(4)研究了微量锗杂质和高浓度碳杂质对直拉硅中Void形成的影响。与CZ硅片相比,GCZ硅片中形成了更高密度的小尺寸Void和更低密度的大尺寸Void,而H[C]CZ硅片中具有更低密度的大尺寸Void,指出这是由于在晶体生长冷却过程中Void形成之前,锗和碳杂质与空位形成复合体从而降低了硅中空位浓度,使得Void形成温度降低所致。此外,微量锗杂质或高浓度碳杂质的引入都可以降低Void的高温热稳定性,这有助于消除硅片近表面区域中的Void,从而提高MOS器件的GOI。(5)研究了微量锗杂质对直拉硅片机械性能的影响,发现掺锗有利于在硅中形成高密度的小尺寸氧沉淀,它们可以钉扎位错从而抑制位错攀移,并由此降低硅片在器件制造过程中的弯曲度和翘曲度,这有利于提高集成电路制造的成品率。(6)根据第一性原理计算,指出直拉硅中的同族元素(锗、碳)杂质可以与空位和间隙氧原子形成复合体。基于实验提供的证据,认为这些复合体可以在晶体生长冷却过程中的高温阶段形成,这一方面消耗了部分空位从而促进高密度小尺寸Void的形成;另一方面,这些复合体在很宽的温度范围内可以作为异质形核核心而促进氧沉淀。同样的,这些复合体也可以在RTA处理的高温过程中形成,并促进后续退火过程中的氧沉淀。在理论和实验工作的基础上,建立了同族元素杂质影响直拉硅中微缺陷(氧沉淀和Void)形成的物理模型。
论文目录
摘要Abstract目录第1章 前言§1.1 研究的背景和意义§1.2 本研究的目的§1.3 本文的结构安排及内容提要第2章 直拉硅单晶的微缺陷及其缺陷工程研究现状§2.1 引言§2.2 直拉硅单晶中的氧和空位2.2.1 直拉硅单晶的生长技术2.2.2 直拉硅单晶中氧的基本性质2.2.3 直拉硅单晶中空位的基本性质§2.3 直拉硅单晶中的氧沉淀2.3.1 直拉硅单晶中氧沉淀的基本性质2.3.2 直拉硅单晶中氧沉淀形成的动力学过程2.3.3 杂质对直拉硅单晶中氧沉淀的影响§2.4 直拉硅片的内吸杂技术2.4.1 基于普通炉退火的内吸杂工艺2.4.2 基于快速热处理的内吸杂技术§2.5 直拉硅单晶中的空洞型缺陷2.5.1 空洞型缺陷的基本性质2.5.2 空洞型缺陷形成的动力学过程2.5.3 杂质对直拉硅单晶中空洞型缺陷的影响§2.6 本文研究方向的提出第3章 实验样品和研究方法§3.1 晶体生长和硅片制备3.1.1 掺锗直拉硅单晶的生长及硅片制备3.1.2 高碳含量的直拉硅单晶的生长及硅片制备§3.2 研究方法3.2.1 退火工艺及热处理设备3.2.2 主要测试方法和测试设备3.2.3 基于第一性原理的计算第4章 掺锗对直拉硅片氧浓度和电学参数的影响§4.1 引言§4.2 实验§4.3 掺锗直拉硅片中的氧杂质浓度分布4.3.1 原生直拉硅片中的氧杂质浓度分布4.3.2 退火直拉硅片中的氧杂质浓度分布§4.4 掺锗直拉硅片中电阻率的分布状况4.4.1 直拉硅片的轴向电阻率分布4.4.2 直拉硅片的径向电阻率分布§4.5 掺锗直拉硅片中少子寿命的分布状况4.5.1 不同导电类型直拉硅片的少子寿命4.5.2 直拉硅片少子寿命径向分布均匀性分析4.5.3 抛光硅片表面的金属含量分析§4.6 本章小结第5章 掺锗对直拉硅片机械性能的影响§5.1 引言§5.2 实验§5.3 掺锗直拉硅片的弯曲度和翘曲度5.3.1 掺锗直拉硅片的主要几何参数5.3.2 掺锗直拉硅片由退火引起的翘曲度§5.4 掺锗对直拉硅片位错滑移的影响5.4.1 原生掺锗直拉硅片表面压痕引起的位错滑移5.4.2 热处理后掺锗直拉硅片表面划痕引起的位错滑移§5.5 掺锗对直拉硅片的断裂强度的影响5.5.1 小尺寸氧沉淀对掺锗直拉硅片的断裂强度的影响5.5.2 大尺寸氧沉淀对掺锗直拉硅片断裂强度的影响§5.6 本章小结第6章 掺锗直拉硅单晶中的氧沉淀§6.1 引言§6.2 实验§6.3 掺锗对直拉硅单晶中原生氧沉淀的影响6.3.1 原生氧沉淀的形成6.3.2 原生氧沉淀的分布特征6.3.3 原生氧沉淀的长大§6.4 掺锗直拉硅单晶低温退火下的氧沉淀6.4.1 低温单步退火中的氧沉淀6.4.2 低-高两步退火中的氧沉淀§6.5 掺锗直拉硅单晶高温退火下的氧沉淀6.5.1 原生硅晶体在高温退火下的氧沉淀6.5.2 消除热历史后的硅晶体在高温退火下的氧沉淀§6.6 掺锗直拉硅单晶中氧沉淀的热稳定性6.6.1 原生氧沉淀的热稳定性6.6.2 氧沉淀在普通炉退火下的热稳定性6.6.3 氧沉淀在快速热退火下的热稳定性§6.7 掺锗影响直拉硅单晶中氧沉淀的机理§6.8 本章小结第7章 掺锗直拉硅片的内吸杂工艺§7.1 引言§7.2 实验§7.3 掺锗直拉硅片中氧杂质的外扩散7.3.1 掺锗直拉硅片中氧杂质的高温外扩散7.3.2 锗促进硅中氧原子外扩散的机理§7.4 掺锗直拉硅片的内吸杂工艺研究7.4.1 高-低-高三步退火内吸杂工艺7.4.2 高温单步退火内吸杂工艺7.4.3 基于快速热处理的内吸杂技术§7.5 掺锗直拉硅片在模拟DRAM制造热工艺中的内吸杂7.5.1 基于普通炉退火的DRAM制造热工艺的模拟7.5.2 具有快速热退火预处理的DRAM制造热工艺的模拟7.5.3 掺锗直拉硅片洁净区和吸杂区的热稳定性7.5.4 掺锗直拉硅片对重金属原子的内吸杂能力§7.6 本章小结第8章 掺锗直拉硅单晶中的空洞型缺陷§8.1 引言§8.2 实验§8.3 掺锗直拉硅片中的晶体原生颗粒8.3.1 锗浓度对掺锗直拉硅片的晶体原生颗粒的影响8.3.2 硼浓度对掺锗直拉硅片的晶体原生颗粒的影响8.3.3 间隙氧浓度对掺锗直拉硅片晶体原生颗粒的影响8.3.4 退火气氛对掺锗直拉硅片晶体原生颗粒消除的影响8.3.5 氢气氛下掺锗直拉硅片晶体原生颗粒退火消除行为§8.4 掺锗直拉硅片中的流动图形缺陷8.4.1 掺锗直拉硅片流动图形缺陷腐蚀工艺参数优化8.4.2 掺锗直拉硅片的流动图形缺陷的径向分布8.4.3 锗浓度对掺锗直拉硅片流动图形缺陷的影响8.4.4 硼浓度对掺锗直拉硅片流动图形缺陷的影响8.4.5 间隙氧浓度对掺锗直拉硅片流动图形缺陷的影响8.4.6 掺锗直拉硅片流动图形缺陷退火消除行为§8.5 掺锗影响直拉硅单晶中空洞型缺陷形成的机理§8.6 本章小结第9章 高碳含量的直拉硅单晶中的氧沉淀§9.1 引言§9.2 实验§9.3 碳对基于CFA的内吸杂工艺过程中氧沉淀的影响9.3.1 普通炉高-低-高三步退火过程中的氧沉淀9.3.2 普通炉Ramping退火过程中的氧沉淀§9.4 碳对基于RTA的内吸杂工艺过程中氧沉淀的影响9.4.1 快速热处理-低-高两步退火过程中的氧沉淀9.4.2 快速热处理-高温单步退火过程中的氧沉淀§9.5 高浓度碳影响直拉硅单晶中氧沉淀的机理§9.6 本章小结第10章 高碳含量的直拉硅片的内吸杂工艺§10.1 引言§10.2 实验§10.3 高碳含量的直拉硅片基于普通炉退火的内吸杂工艺10.3.1 洁净区的形成10.3.2 洁净区的热稳定性§10.4 高碳含量直拉硅片基于Ramping退火的内吸杂工艺10.4.1 低温Ramping单步退火中洁净区的形成10.4.2 高温-低温Ramping两步退火中洁净区的形成§10.5 高碳含量的直拉硅片基于快速热处理的内吸杂工艺10.5.1 基于快速热处理的洁净区形成工艺10.5.2 快速热处理工艺形成洁净区过程中的影响因素§10.6 本章小结第11章 高碳含量的直拉硅单晶中的空洞型缺陷§11.1 引言§11.2 实验§11.3 高碳含量的直拉硅片中的原生流动图形缺陷§11.4 高碳含量的直拉硅片流动图形缺陷普通炉退火行为11.4.1 CFA退火温度对流动图形缺陷的影响11.4.2 CFA退火时间对流动图形缺陷的影响11.4.3 CFA保护气氛对流动图形缺陷的影响§11.5 高碳含量的直拉硅片流动图形缺陷快速热退火行为11.5.1 RTA退火温度对流动图形缺陷的影响11.5.2 RTA退火时间对流动图形缺陷的影响11.5.3 RTA退火后的冷却速率对流动图形缺陷的影响§11.6 高浓度碳影响直拉硅单晶空洞型缺陷形成的机理§11.7 本章小结第12章 同族元素掺杂直拉硅单晶中复合体和微缺陷形成的理论依据和物理模型§12.1 引言§12.2 计算模型和实验方案§12.3 掺锗直拉硅单晶中的锗关复合体12.3.1 锗-空位复合体12.3.2 锗-空位-氧复合体§12.4 高碳含量的直拉硅单晶中的碳关复合体12.4.1 碳-空位复合体12.4.2 碳-空位-氧复合体§12.5 同族元素杂质影响直拉硅单晶中微缺陷的机理§12.6 本章小结第13章 总结与展望§13.1 主要创新性结果§13.2 未来工作展望参考文献致谢附录:攻读博士学位期间取得的科研成果
相关论文文献
- [1].基于数值模拟的太阳能直拉硅单晶热场降耗研究[J]. 稀有金属材料与工程 2016(11)
- [2].直拉硅单晶生长过程建模与控制研究综述[J]. 控制理论与应用 2017(01)
- [3].横向磁场中直拉硅单晶生长[J]. 电子工业专用设备 2016(07)
- [4].中国科学院上海硅酸盐研究所研发成功4英寸碳化硅单晶[J]. 人工晶体学报 2013(02)
- [5].上海硅酸盐研究所研发成功4英寸碳化硅单晶[J]. 功能材料信息 2013(01)
- [6].硅单晶切割的初步探索[J]. 现代制造技术与装备 2017(05)
- [7].直拉硅单晶炉热系统的改造对氧、碳含量的影响[J]. 湖南科技大学学报(自然科学版) 2009(03)
- [8].液面位置对Φ300mm硅单晶固液界面形状影响的数值计算[J]. 人工晶体学报 2008(06)
- [9].直拉硅单晶的杂质工程:微量掺锗的效应[J]. 中国科学:信息科学 2019(04)
- [10].水平磁场下18英寸直拉硅单晶生长工艺的三维数值模拟[J]. 稀有金属 2017(03)
- [11].大直径重掺硼硅单晶生长工艺研究[J]. 电子工业专用设备 2015(08)
- [12].碳/碳复合材料应用于直拉硅单晶生长的研究[J]. 电子工业专用设备 2011(04)
- [13].φ200mm太阳能电池用直拉硅单晶生长中导流系统的研究[J]. 半导体学报 2008(09)
- [14].直拉硅单晶热场加热器设计分析[J]. 炭素技术 2013(06)
- [15].直拉硅单晶放肩过程的有限元数值模拟与控制参数研究[J]. 人工晶体学报 2013(01)
- [16].中科院上海硅酸盐所研发出4英寸碳化硅单晶[J]. 材料导报 2013(05)
- [17].中科院上海硅酸盐所研发出4英寸碳化硅单晶[J]. 硅谷 2013(04)
- [18].氧沉淀对直拉硅单晶硬度的影响[J]. 稀有金属 2009(05)
- [19].不同选点方案下硅单晶薄层径向电阻率变化[J]. 电子工业专用设备 2017(06)
- [20].直拉硅单晶宽面控制工艺研究[J]. 天津科技 2017(11)
- [21].直拉重掺硼硅单晶的碱腐蚀特性研究[J]. 电子工业专用设备 2013(09)
- [22].消除区熔硅单晶生长中“硅刺”的研究[J]. 电子工业专用设备 2012(05)
- [23].拉晶工艺中直拉硅单晶氧含量的优化研究[J]. 太阳能 2010(11)
- [24].气相掺杂区熔硅单晶的掺杂剂量计算方法研究[J]. 电子工业专用设备 2013(10)
- [25].空位对普通和掺氮直拉硅单晶中氧沉淀形核的作用[J]. 半导体学报 2008(10)
- [26].高线速下碳化硅单晶的快速平坦化切割[J]. 超硬材料工程 2019(01)
- [27].区熔硅单晶生长过程建模综述[J]. 电子工业专用设备 2018(03)
- [28].中电二所“三代半导体碳化硅单晶产业化”项目通过验收[J]. 科技创新与生产力 2015(12)
- [29].硅单晶电阻率四探针法测量不确定度评定[J]. 中国计量大学学报 2016(03)
- [30].6英寸重掺砷硅单晶及抛光片[J]. 中国集成电路 2008(05)
标签:直拉硅论文; 微缺陷论文; 氧沉淀论文; 空洞型缺陷论文; 缺陷工程论文; 掺锗论文; 掺碳论文;
大规模集成电路用同族元素掺杂直拉硅单晶的微缺陷及其缺陷工程
下载Doc文档