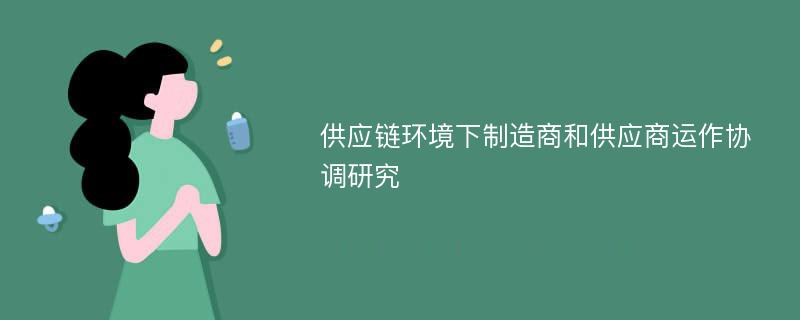
论文摘要
本论文就制造商和供应商在物料供应运作环节的协调和优化进行了深入的研究。物料供应运作的起点是制造企业的生产对物料的需求,制造商是物料补货流程运作协调的主体。物料补货流程中的决策包括三个方面:一、物料补货流程的基本框架和规模----由制造商决定的以供应商数量的决策为核心的供应基础规模问题和采购方式问题;二、以补货量的确定为核心的物料补货批量和频率的补货优化问题;三、物料补货流程的协调和优化问题。供应基础规模的大小取决于减少供应商数量带来的利益增加和风险增加之间的平衡。论文构建了基于利益和风险平衡的供应商数量优化模型。对最优供应商数量的分析表明:零部件的标准化程度,供应商的生产规模效应和正激励反馈程度及其对制造商的影响和供应商数量之间呈反向关系,供应商数量和供应风险之间的关系是正向的,因此供应基础决策和制造商的风险规避战略有关。JIT采购和EOQ采购模式的成本优势分别在于前者的低库存、低空间占用和后者的生产、运输规模效应。论文分析了两种模式下的生产启动成本、存储空间成本、单位库存成本、订购成本、信息投入成本、运输成本,给出了选择JIT或者EOQ采购的成本差异模型。论文分别构建了单产品-单供应商,单产品-多供应商和多产品-单供应商情况下的补货批量优化模型。在补货优化模型中,为了更准确的反映订货成本的构成,论文区分了订单成本中的固定成本和可变成本,订货成本中固定成本分离的订货量比未分离时小;模型从制造商和供应商整体角度考虑的订货决策优化,优于买卖各方的单独决策;模型完整的考虑了补货运作中的订单成本、库存成本、运输成本,物料处理能本;和传统模式的经济订购批量相比,模型得到的最优订货批量比制造商单独决策时的订购批量要大,这是因为考虑到了供应商的库存成本和订货成本。考虑到运输成本的规模效益,这个订购批量变得更大;论文细分了不同生产模式的补货特点,进一步深入研究MTP、MTO、ATO模式下的补货批量优化。MTO模式中需要满足生产规模和时间的约束,采购成本优化不再是唯一目的。在考虑多产品、单供应商时,补货决策包含两个层次的优化:订货批量优化和订单合并优化,论文构建了基于0-1规划的JOP模型来解决订单合并的优化问题,JOP模型的研究方法和研究思路和传统的JRP模型完全不同,能更直观、准确的解决一般订单合并问题,具有普适性。在对订货流程的协调上,信息协调成为重要的协调方式。信息技术直接促进了交易效率和运作效率的提高,以信息技术为基础的信息共享和沟通起着减少库存和支持决策的作用,以预测、计划和共同安排的更高层次的战略信息合作对全局起着指导作用。从流程协调的另一方面而言,以流程作业的价值增值出发的作业成本分析成为作业流程平衡、改进的协调依据。
论文目录
致谢摘要Abstract1 绪论1.1 研究背景1.1.1 生产制造方式的革新1.1.2 信息技术快速发展1.1.3 管理理念的发展1.2 供应链协调1.3 国内外研究综述1.3.1 供应链协调研究综述1.3.2 制造商和供应商运作整合协调研究综述1.3.3 供应链协调理论研究总结1.4 选题依据和研究意义1.4.1 选题的实际意义1.4.2 选题的理论意义1.5 论文的内容和结构安排2 供应链运作协调理论基础2.1 基于资源的观点(Resource-based View)2.1 交易成本理论2.3 系统理论2.4 本章小结3 制造商和供应商的运作协调3.1 制造商和供应商运作协调涵义3.1.1 本文对制造商和供应商运作协调含义的界定3.1.2 制造商和供应商运作流程协调目标3.2 制造商和供应商运作协调的层次3.3 物料供应决策框架3.3.1 以制造商物料需求驱动为主体的供应决策3.3.2 供应商运作流程协调框架3.4 运作流程同步分析3.4.1 制造商和供应商之间的业务运作流程3.4.2 运作同步性措施3.5 本章小结4 供应基础优化模型4.1 供应基础4.1.1 供应商评估和选择4.1.2 供应商数量决策4.2 供应基础规模4.2.1 供应商数量减少的趋势4.2.2 供应风险4.3 考虑供应风险和供应商订货激励的供应商数量优化模型4.3.1 基本假设4.3.2 供应商数量激励4.3.3 供应激励和风险平衡的数量优化模型4.4 小结5 供应商与制造商物料补货决策5.1 供应商与制造商的补货运作流程5.1.1 供应商与制造商的补货运作流程5.1.2 运作流程与生产类型的一致性5.2 补货运作中的订购成本修正5.2.1 订货成本结构的变化5.2.2 固定成本分离的EOQ修正5.3 两种基本采购决策: EOQ 和 JIT5.3.1 决定采购模式的成本差异模型5.3.2 数值分析5.4 单产品、单供应商补货决策5.4.1 基本补货模型5.4.2 考虑运输成本的改进模型5.4.3 基于生产方式的补货决策5.5 单产品、多供应商补货决策5.5.1 基本补货决策5.5.2 单产品、多供应商的第三方物流选择模型5.5.3 MTO 模式下的单产品、多供应商补货模型5.6 多产品,单供应商订货决策5.6.1 相关文献回顾5.6.2 多产品、单个供应商订单合并模型5.6.3 JOP 模型和 JRP 模型的对比分析5.7 本章小结6 物料补货运作流程协调6.1 物料补货运作流程6.2 物料补货运作流程协调6.2.1 流程协调和优化原则6.2.2 流程优化方法6.2.3 流程协调的范例6.2.4 补货运作流程协调框架6.3 补货运作流程信息协调6.3.1 运作信息协调6.3.2 信息技术协调6.3.3 信息协调模型6.4 基于ABCM 和模糊综合评价的补货运作流程改进模型6.4.1 作业成本管理6.4.2 补货运作流程改进模型6.5 本章小结7 应用实例研究7.1 徐工科技的经营管理基本情况7.1.1 徐工科技基本情况7.1.2 徐工科技经营情况7.2 徐工科技的物料采购环节基本情况7.3 徐工科技的物料运作流程研究7.3.1 徐工的物料采购决策和补货运作流程7.3.2 徐工的物料采购补货运作流程存在的问题及相应对策7.4 徐工的物料订购决策研究7.5 本章小结8 结论与展望8.1 本文的主要结论8.2 本文的创新之处8.3 研究展望参考文献附录一附录二作者简历学位论文数据集
相关论文文献
标签:供应链论文; 协调论文; 运作论文; 补货流程论文;