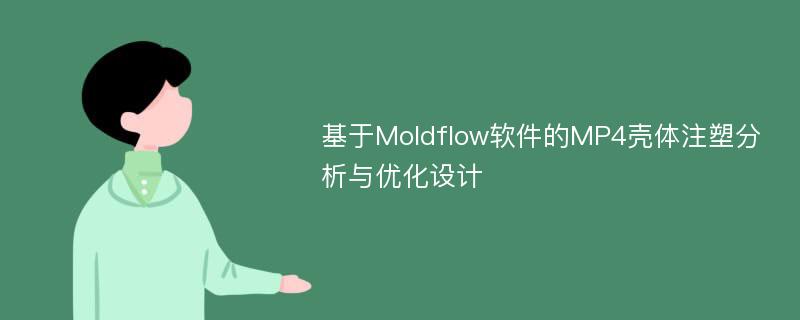
论文摘要
随着现代工业的飞速发展,模具工业日益受到人们的重视和关注。注塑模具是塑料模具的重要组成部分。在注塑成型实际生产过程中,由于众多复杂因素的影响,设计人员很难预测出制件上出现的缺陷,因此要经过多次的试模、修模、调整工艺条件才能投入生产。如今,该种方法已不能满足快速生产的需要,CAE技术凭借自身优势,已经成为注塑模具设计中不可或缺的一部分。本课题利用最常用的模具CAE软件—Moldflow,对原始设计方案进行流动、冷却、翘曲三方面的模拟分析,模拟出型腔中塑料熔体的流动、保压和冷却过程,并通过原始设计方案的分析结果,预测出制件在流动和翘曲方面上的缺陷。针对制件在熔接痕和收缩变形上的缺陷,列举出的缺陷产生的原因和解决办法。首先利用最佳浇口位置模块进行浇口位置的优化设计,改善了制件熔接痕的大小和位置,然后利用软件中的成型工艺窗口模块分析出最佳的成型工艺条件,优化后收缩变形量略微有所减小,最后利用对保压曲线的优化设计,将变形量降低到规定范围内。本文的研究成果对于提出合理的注塑成型方案具有十分重要的指导意义。同时。为针对复杂注塑模具设计利用Moldflow软件进行有限元分析,探索出一条切实可行的途径。
论文目录
中文摘要ABSTRACT第一章 塑料模具中的CAE 技术1.1 注塑成型CAE 技术的研究现状1.1.1 充填/保压模拟模块1.1.2 冷却模拟模块1.1.3 残余应力与翘曲变形分析模块1.2 CAE 技术在塑料模具中的应用1.3 注塑成型CAE 技术存在的主要问题1.4 课题的背景及主要研究内容1.4.1 课题的背景1.4.2 课题研究的主要内容第二章 Moldflow 分析基础2.1 注塑成型过程及成型工艺条件2.1.1 注塑成型过程2.1.2 注塑成型的工艺条件2.2 注塑成型充填过程熔接痕形成的数学模型2.3 翘曲变形的数学模型2.4 本章小结第三章 原始方案注塑过程模拟分析3.1 制件的结构分析与有限元网格模型的建立3.2 分析类型的选择与成型材料的选择3.2.1 分析类型的选择3.2.2 成型材料的选择3.3 原始浇注系统和冷却系统方案设计3.3.1 原始浇注系统方案设计3.3.2 原始冷却系统方案设计3.4 注塑工艺参数的设置3.4.1 注塑工艺参数对注塑成型的影响3.4.2 工艺过程参数的设置3.5 分析计算与原始方案注塑过程模拟结果分析3.5.1 流动结果分析3.5.2 冷却结果分析3.5.3 翘曲分析3.6 本章小结第四章 原始方案的优化设计4.1 原始方案的缺陷分析4.1.1 熔接痕产生的原因及解决办法4.1.2 翘曲变形产生的原因及解决办法4.2 浇口位置优化设计4.2.1 浇口位置的选择原则4.2.2 最佳浇口位置的确定4.2.3 浇口位置的改进方案与改进后的熔接痕结果分析4.3 成型工艺的优化设计4.3.1 成型工艺窗口分析4.3.2 成型工艺改进后的翘曲变形分析结果4.4 保压曲线的优化设计4.4.1 保压曲线的调整4.4.2 保压曲线改进后的翘曲变形分析结果4.5 本章小结第五章 优化设计后注塑过程模拟分析5.1 分析前处理5.1.1 优化后的浇注系统5.1.2 优化后的工艺过程参数设置5.2 优化后方案注塑过程模拟结果分析5.2.1 流动结果分析5.2.2 冷却结果分析5.2.3 翘曲分析5.3 本章小结第六章 结论与展望6.1 结论6.2 展望参考文献致谢
相关论文文献
标签:注塑成型论文; 熔接痕论文; 翘曲论文; 优化设计论文; 壳体论文;
基于Moldflow软件的MP4壳体注塑分析与优化设计
下载Doc文档