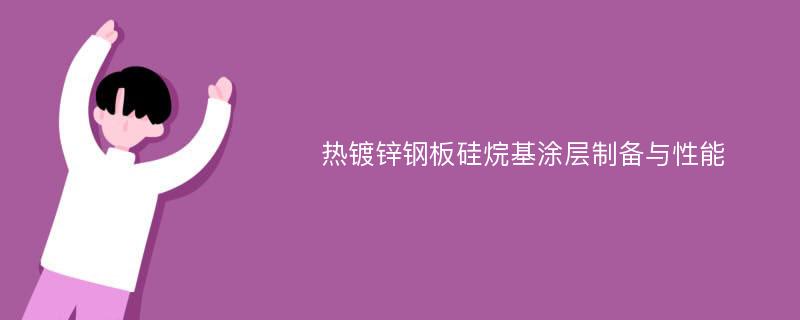
论文摘要
锌被大量用做钢的防腐蚀保护层。因为钢和锌层之间存在大的电位差,所以锌的溶解速率很高。在潮湿的环境中热镀锌钢板易发生腐蚀,使其表面形成白色的腐蚀产物或变成灰暗色,影响了热镀锌钢板的外观质量和镀层抗腐蚀性。为了降低锌在腐蚀性介质中的溶解速率,对热镀锌钢板广泛采用铬酸盐钝化的处理工艺。然而,六价铬酸盐属于极毒、致癌性物质、具有诱变作用。为满足环境友好型热镀锌表面处理钢板的需求,无铬热镀锌处理钢板的开发和生产逐渐得到重视,并取得了较快发展。本文研制开发以无毒、无污染的双-[γ-(三乙氧基硅)丙基]四硫化物硅烷(BTESPT)、γ-氨丙基三乙氧基硅烷(y-APS)为主要成分,以无机添加剂为辅助的有机/无机复合处理体系。通过单因素实验,利用醋酸铅点滴实验、中性盐雾实验等加速腐蚀试验手段对硅烷BTESPT处理液配方进行了设计和筛选,系统研究了硅烷BTESPT处理液的组成成分及用量,确定了硅烷BTESPT处理液的基本组成为:BTESPT5vol.%,水14vol.%,乙酸0.5vol.%,乙醇81vol.%,处理液水解温度为35℃。依据中性盐雾实验等级标准,运用对比实验方法对稀土硝酸盐、纳米级氧化物以及缓蚀剂等添加剂的种类、用量进行了研究,确定硅烷BTESPT处理液的改性添加剂及用量分别为硝酸铈O.OOlmol/L,硅溶胶0.005-0.02g/L,苯并三氮唑0.001g/L运用对比和正交实验方法对浸渍时间、处理液水解时间、固化时间及固化温度等工艺参数进行了确定,并研究了工艺参数变化对硅烷涂层性能的影响。结果表明,在工艺参数为:处理液水解时间72h,浸渍时间5s,固化温度120℃,固化时间30min时,硅烷BTESPT涂层具有良好的耐蚀性。运用Tafel极化曲线和EIS交流阻抗谱的腐蚀电化学方法测试了硅烷涂层的腐蚀性能。结果表明,经过BTESPT硅烷处理后的热镀锌试样的腐蚀极化过程是阳极控制型,自腐蚀电位明显的正移,自腐蚀倾向显著的降低;交流阻抗谱为第一象限两个半径较大的的容抗弧,在低频区未出现斜率为1的直线,腐蚀体系受电化学控制。利用傅立叶红外反射光谱FTIR分析了硅烷处理层的结构,结果表明硅烷处理层中含有SiOH、Si-O-Si、Si-O-Zn、CH2、-SiO-等主要有机官能团。利用XPS光电子能谱分析了硅烷BTESPT处理层的元素组成及存在形式。XPS分析结果表明,硅烷BTESPT处理层含有C、O、Si、S、Zn等元素。经Ar+射深度和成膜元素的窄幅扫描结果显示,硅烷BTESPT处理层的最外层可能为SiOH、Si-O-Si、Si-O-等结构,内层可能为Si-O-Si、Si-O-Zn等结构,界面层可能为ZnO、ZnS、ZnSiO3等化合物。硅烷BTESPT处理层的厚度约为200nm。采用电子显微镜、金相显微镜观察了硅烷BTESPT处理层的表面微观形貌。在微观形貌分析中发现硅烷BTESPT处理层的表面均匀、致密、完整、纳米结构,但存在一些微裂纹。通过加入稀土硝酸铈、硅溶胶、苯并三氮唑(BTA)添加剂改性硅烷BTESPT处理液后,弥补并减少了裂纹的进一步产生。由于铈的氧化物或氢氧化物、惰性硅酸盐膜等不溶性物质沉积或填充Si-O-S、Si-O-Zn的网络结构,使硅烷BTESPT涂层更致密,减少了外界O2、H2O、Cl-等腐蚀性物质接触金属锌的机会,抑制了锌的电化学腐蚀反应,因此大大提高了硅烷BTESPT涂层的抗蚀性。以1级中性盐雾实验标准为依据,通过对比实验确定了BTESPT/y-APS混合硅烷处理液的组成成分:硅烷BTESPT1-4vol.%,硅烷y-APS2-4vol.%,水量28vol.%,其余为乙醇,pH值4-6。由于硅烷γ-APS结构中含有-NH2亲水基团,促进硅烷BTESPT充分水解的同时,又能抑制硅醇的缩合,从而使耐蚀性显著提高。
论文目录
摘要ABSTRACT目录第一章 绪论1.1 热镀锌1.2 铬酸盐钝化1.2.1 六价铬钝化1.2.2 三价铬钝化1.3 无铬钝化1.3.1 钼酸盐、磷/钼酸盐钝化处理1.3.2 硅酸盐钝化处理1.3.3 稀土盐钝化处理1.3.4 钨酸盐、钛、锆、铪系钝化处理1.3.5 有机酸钝化处理1.3.6 硅烷钝化处理1.3.7 有机钼酸盐钝化处理1.3.8 树脂基无机掺杂钝化处理1.4 镀锌层无铬钝化技术的意义及存在问题1.5 本论文研究的目的和研究内容参考文献第二章 实验材料和实验方法2.1 实验材料2.1.1 实验原材料2.1.2 实验用仪器及设备2.2 实验过程2.2.1 脱脂2.2.2 预处理2.3 处理液的研制2.3.1 单硅烷体系处理液的研制2.3.2 混合硅烷体系处理液的研制2.4 预处理工艺参数的确定2.5 硅烷涂层的性能测试2.5.1 硅烷涂层的表征2.5.2 硅烷涂层耐蚀性能测试2.6 硅烷涂层附着力试验2.6.1 硅烷涂层与基体附着力试验2.6.2 硅烷涂层与底漆的附着力试验参考文献第三章 单硅烷体系各组分对涂层性能影响3.1 硅烷(SA)试剂的选择及用量确定3.1.1 硅烷(SA)试剂的选择3.1.2 硅烷BTESPT试剂的水解3.1.3 硅烷BTESP试剂水解的红外光谱分析(FTIR)3.1.4 硅烷BTESPT试剂浓度变化对耐蚀性的影响3.2 溶剂的选择3.3 水量的确定3.4 PH调节剂的选择及确定3.4.1 pH调节剂的选择3.4.2 硅烷BTESPT处理液pH调节剂用量的确定3.5 硅烷BTESPT处理液中各组分的优化3.5.1 优化配方的确定3.5.2 硅烷BTESPT处理液的稳定性研究3.6 硅烷G-APS涂层性能的简单研究3.6.1 γ-APS处理液的配制及涂层的制备3.6.2 γ-APS硅烷膜的表征3.6.3 γ-APS涂层的耐蚀性能研究3.6.4 γ-APS硅烷膜的XPS分析3.7 本章小结参考文献第四章 不同添加剂对硅烷涂层耐蚀性的影响4.1 稀土盐类掺杂剂4.1.1 硝酸铈对涂层性能的影响4.1.2 硝酸镧对涂层性能的影响4.1.3 稀土硝酸盐对涂层性能的比较研究4.1.4 硝酸铈掺杂BTESPT硅烷膜的表征4.1.5 硝酸铈掺杂处理耐蚀机理4.2 纳米级氧化物类掺杂4.2.1 纳米级氧化锆掺杂对涂层性能的影响4.2.2 纳米级氧化铝掺杂对涂层性能的影响4.2.3 硅溶胶掺杂对涂层性能的影响4.2.4 纳米级氧化锆、硅溶胶耐蚀性对比研究4.2.5 硅溶胶改性BTESPT涂层耐蚀机制研究4.3 缓蚀添加剂4.3.1 缓蚀剂的定义、分类、缓蚀效率4.3.2 苯并三氮唑(BTA)缓蚀添加剂4.3.3 三乙醇胺(TEA)缓蚀添加剂4.4 本章小结参考文献第五章 工艺参数对硅烷涂层耐蚀性影响5.1 工艺参数的确定5.1.1 处理液水解时间对硅烷涂层耐蚀性影响5.1.2 处理液水解温度对硅烷涂层耐蚀性影响5.1.3 浸渍时间对硅烷涂层耐蚀性影响5.1.4 固化对硅烷涂层耐蚀性影响5.2 各工艺参数的优化5.3 处理液性能研究5.3.1 耐蚀性对比实验5.3.2 硅烷涂层附着力初步研究5.4 本章小结参考文献第六章 硅烷处理成膜机理与耐蚀性6.1 机理概述6.1.1 钝化理论6.1.2 硅烷的作用机理6.2 硅烷涂层腐蚀电化学分析6.2.1 硅烷涂层的Tafel极化曲线6.2.2 硅烷涂层的电化学交流阻抗(EIS)分析6.3 硅烷膜FTIR分析6.4 硅烷膜XPS分析6.4.1 硅烷BTESPT处理膜的全元素扫描6.4.2 硅烷BTESPT处理膜的窄幅扫描6.5 硅烷涂层的耐蚀性分析6.5.1 硅烷涂层的成膜过程分析6.5.2 硅烷涂层的耐蚀机理分析6.6 本章小结参考文献第七章 混合硅烷体系各组分对处理层性能影响7.1 确定混合硅烷处理液组成及用量7.1.1 混合硅烷处理液的制备7.1.2 硅烷γ-APS用量的确定7.1.3 硅烷BTESPT用量的确定7.1.4 水用量的确定7.1.5 pH值的确定7.2 混合硅烷膜层的表征7.3 混合硅烷涂层的电化学分析7.4 混合硅烷膜层的XPS分析7.5 本章小结参考文献第八章 结论创新说明工作展望攻读博士学位期间发表的论文攻读博士学位期间申请的专利致谢个人简历
相关论文文献
标签:硅烷论文; 无铬处理论文; 热镀锌钢板论文; 添加剂论文; 耐蚀性能论文;