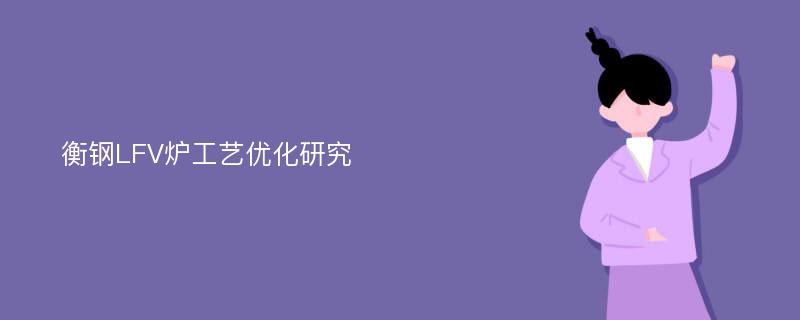
论文摘要
衡钢40tLFV炉自1991年投产以来,由于设备和工艺不完善,脱硫、脱氧、脱气和去除夹杂物等精炼效果一直不太理想。本文在现场调研的基础上,从改善LFV炉精炼的热力学和动力学条件入手,经过充分论证,通过冷态水力模拟实验优化供氩参数;采用改进的复合精炼渣和工艺参数,通过工业性试验在线优化LFV炉生产工艺,强化LFV精炼功能,取得了显著的深度脱氧、脱硫、脱气和良好的去夹杂效果。论文对衡钢LFV精炼传统工艺进行了全面深入的分析与评价,找出了问题。针对其中的以技术性为主的问题,在精炼试验中进行了解决,并对整个工艺进行了优化和改进。水模试验及相应的研究表明,衡钢LFV炉应采取分阶段变流量的吹氩模式。LFV精炼工业性试验研究表明,采用1#CaO-Al2O3渣系和2#CaO-BaO渣系能够达到良好的深度脱氧、脱硫效果,精炼渣加入量为钢水量的0.8%~1.3%;最大加热功率为6000KW,平均吹氩时间为105min。研究认为:衡钢LFV炉已具备发挥其精炼功能的条件,只要优化工艺制度,进一步改造设备,加强规范化操作,衡钢LFV炉同时脱氧、脱硫、脱气的功能可以充分体现。
论文目录
摘要ABSTRACT第一章 文献综述1.1 LFV技术历史与现状1.1.1 LFV技术发展背景1.1.2 国内外LFV技术历史与现状1.2 LFV精炼功能1.2.1 炉内气氛1.2.2 氩气搅拌1.2.3 埋弧加热1.2.4 白渣或造高碱度还原渣精炼1.2.5 合金元素微调与化学成分控制1.2.6 真空脱气1.3 LFV精炼工艺和效果1.3.1 LF基本精炼工艺的实现1.3.2 LF炉处理的钢种、处理时间和电耗1.3.3 LFV炉精炼效果1.3.4 LFV炉精炼对钢水成分的影响1.4 LFV设备及其相关技术1.4.1 LFV的设备特点1.4.2 LF相关技术1.5 衡钢LVF炉历史1.5.1 衡钢概况1.5.2 衡钢LFV炉历史1.6 课题的提出第二章 LFV精炼基本原理2.1 脱氧2.1.1 LF炉可采用的脱氧方法2.1.2 影响LF炉脱氧的因素2.1.3 LF炉脱氧的优势2.2 脱硫2.2.1 LF脱硫热力学2.2.2 LF脱硫动力学2.2.3 影响LF炉脱硫的因素2.2.4 LF炉脱硫的优势2.3 LF炉气体行为2.3.1 LF炉气体行为对钢液中氢的影响2.3.2 LF炉气体行为对钢液中氮的影响2.3.3 LF炉气体行为对钢液中夹杂的影响2.4 真空下的气体行为2.5 钢中夹杂含量第三章 电炉钢的LFV精炼3.1 电炉—控制出钢下渣量3.2 LFV炉—尽快形成高碱度还原性精炼渣3.3 强化预脱氧3.4 强化还原气氛下的吹氩搅拌3.5 真空下的脱气3.5.1 真空脱气热调试前的生产准备3.5.2 对蒸汽要求3.5.3 抽真空时间和LF炉钢水温度要求3.5.4 吹氩流量3.5.5 脱氧方式3.5.6 最高真空度及保持时间3.5.7 生产实践及效果3.6 实现精炼过程自动化第四章 衡钢LF精炼传统工艺分析4.1 设备和工艺中的问题与不足4.2 传统工艺分析4.2.1 加热时间、吹氩时间和精炼周期4.2.2 升温速度4.2.3 脱硫效果4.2.4 炉渣碱度和(FeO)含量4.2.5 [O]、[N]含量与脱氧效果4.2.6 非金属夹杂物尺寸、数量和级别4.3 分析小结第五章 40T钢包底吹氩水力模拟试验5.1 吹氩技术发展简史5.2 钢水吹氩处理的功能5.3 衡钢吹氩参数5.4 试验目的5.5 研究方法—相似原理5.5.1 几何相似5.5.2 物理相似5.5.3 动力相似5.6 模拟实验5.6.1 实验装置5.6.2 试验方案5.6.3 试验结果5.7 分析与讨论5.7.1 底吹气搅拌时钢一渣的运动特征5.7.2 影响吹Ar搅拌效果的因素5.7.3 吹Ar搅拌强度—比搅拌能5.8 实验小结第六章 LF精炼试验6.1 试验方案设计6.1.1 造渣6.1.2 加料6.1.3 吹氩6.1.4 升温6.1.5 精炼时间6.2 试验操作6.2.1 低碳系列钢(圆坯水平连铸)6.2.2 中碳系列钢(圆坯水平连铸)6.3 试验结果及分析6.3.1 试验结果6.3.2 结果分析6.4 试验小结第七章 结论7.1 底吹氩水力模拟试验结论7.2 LF精炼工业性试验结论参考文献致谢攻读工程硕士期间发表的论文
相关论文文献
标签:精炼论文; 吹氩论文; 脱氧论文; 脱硫论文; 脱气论文;